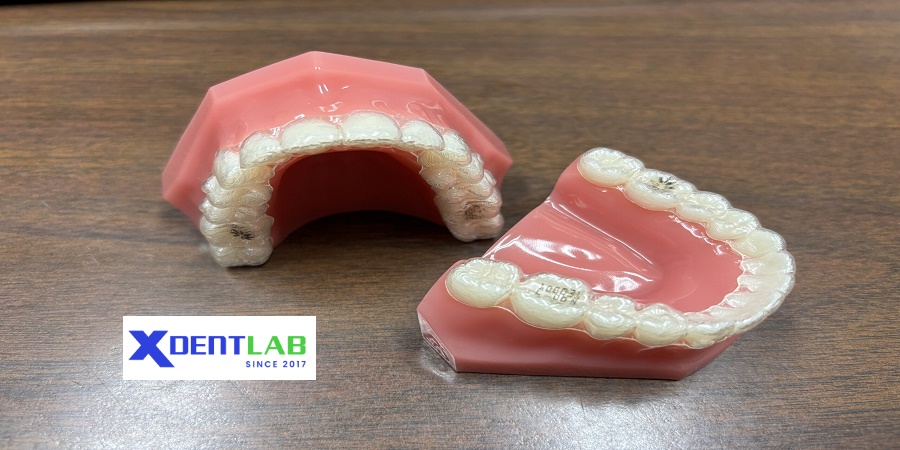
Top clear aligners manufacturing xdentlab.com Clear aligners represent a modern approach to orthodontic treatment, providing a discreet and comfortable alternative to traditional metal braces. These custom-made, transparent trays are designed to gradually shift teeth into their desired positions, resulting in improved alignment and a more aesthetically pleasing smile. Made from a flexible thermoplastic material, clear aligners are tailored to the unique dental structure of each patient, ensuring a precise fit and optimal comfort during wear.
Introduction to Clear Aligners
The efficacy of clear aligners is rooted in their design and technology. Using advanced 3D computer imaging and treatment planning, orthodontists can create a series of aligners, each representing a step in the tooth movement process. Patients typically progress from one aligner to the next approximately every two weeks, enabling a gradual and controlled adjustment over time. The ability to visualize the treatment plan in advance has increased the confidence of both orthodontists and patients in using clear aligners as a reliable solution for teeth alignment.
Over the past few years, clear aligners have gained remarkable popularity among individuals seeking orthodontic treatment. Factors contributing to this trend include their unobtrusive nature, ease of maintenance, and the increased comfort they provide compared to traditional braces. The convenience of being able to remove the aligners while eating or brushing is a notable advantage that appeals to many patients. Consequently, clear aligners have become a mainstream option in orthodontics, allowing patients to engage in treatment without the visibility and limitations associated with metal brackets and wires.
In recent times, Vietnam dental laboratory technology has played a significant role in enhancing the effectiveness and acceptance of clear aligners. Innovations such as improved materials, expanded digital capabilities, and tailored software for treatment planning have led to more efficient and predictable outcomes. As clear aligners continue to evolve, their position in the orthodontic landscape is likely to grow stronger, catering to the diverse needs and preferences of patients worldwide.
The Clear Aligners Manufacturing Process
The manufacturing of clear aligners involves a meticulous and technology-driven process that ensures each set of aligners is tailored to the unique dental structure of the patient. The journey begins with an initial patient assessment conducted by an orthodontist, who evaluates the patient’s dental health and suitability for aligner treatment. Following this assessment, a detailed digital scan of the patient’s teeth is obtained using advanced intraoral scanning technology. This technique captures high-resolution images, allowing for the creation of a precise 3D model of the dental arch.
Once the digital model is created, orthodontists utilize specialized software to develop a comprehensive treatment plan. This plan outlines the necessary movements for each tooth throughout the treatment course. Based on this blueprint, a series of aligners, typically made from a clear thermoplastic material, are designed. The choice of materials is critical, as they must exhibit both strength and flexibility while being comfortable for the patient.
After the digital designs are finalized, 3D printing technology comes into play. High-resolution 3D printers create the molds for the aligners, ensuring accuracy in dimensions and fit. Post-printing, the aligners undergo a finishing process where they are trimmed and polished to eliminate any irregularities caused during manufacturing. Each aligner in the series is produced sequentially based on the planned movements and is labeled for patient use. This precision in manufacturing, facilitated by innovative technologies, enables clear aligners to effectively guide teeth into their desired positions.
Ultimately, the integration of cutting-edge technology in clear aligners manufacturing culminates in a product that not only meets the aesthetic desires of patients but also delivers effective orthodontic outcomes. The combination of digital planning, precise 3D printing, and careful finishing contributes to the revolution in orthodontic treatments, making clear aligners a preferred option for many patients.
Materials Used in Clear Aligner Production
Clear aligners are a breakthrough in orthodontics, offering patients a discreet method for teeth straightening. One of the fundamental aspects contributing to their effectiveness and user comfort is the variety of materials employed in their production. At the forefront is medical-grade thermoplastic, which has gained immense popularity due to its unique properties. These materials are designed specifically for dental applications, ensuring biocompatibility with the oral environment.
Among the prominent thermoplastics used in clear aligner manufacturing, polyurethane and polyethylene terephthalate glycol (PETG) are particularly noteworthy. Polyurethane is known for its excellent flexibility and elasticity, enabling the aligners to apply controlled forces to the teeth without causing discomfort. This property is vital as it allows for the seamless movement of teeth throughout the treatment process. PETG, on the other hand, is celebrated for its clarity and strength. The superior transparency of PETG is crucial for aesthetic appeal, as patients often desire aligners that are barely noticeable while accommodating their lifestyle.
Moreover, these materials possess high durability and resistance to staining, ensuring that the aligners maintain their pristine appearance even after extended wear. The ability to withstand daily wear and tear means patients can enjoy their daily activities without concern for damage. Additionally, the inherent comfort of medical-grade thermoplastics allows for an improved user experience, as the aligners fit snugly against the dental arch, reducing irritation to the gums and soft tissues.
In conclusion, the selection of materials in clear aligner production is of paramount importance. The combination of medical-grade thermoplastics not only enhances the effectiveness of the treatment but also prioritizes patient comfort and satisfaction, thereby establishing clear aligners as a revolutionary option in modern orthodontics.
Quality Control in Manufacturing
The manufacturing process for clear aligners is critical to ensuring that the final product is safe, accurate, and durable. Quality control (QC) plays a vital role in this process, as it involves systematic monitoring and evaluation of various manufacturing stages. Manufacturers need to adhere to strict standards and regulations set forth by both national and international bodies, Vietnam dental laboratories ensuring that the aligners meet all safety and performance criteria. These regulations may include compliance with ISO standards and specific dental industry guidelines that govern the production of orthodontic devices.
In order to maintain high-quality output, manufacturers incorporate various testing methods throughout the production process. Initial material assessments are conducted to verify that the raw materials used in making the aligners meet the necessary specifications. Subsequently, during the manufacturing phase, regular inspections are performed to assess the integrity of each aligner at every step. This includes monitoring the digital scanning, 3D printing, and molding processes, ensuring that deviations are identified and rectified promptly.
Final product testing is equally essential in establishing the efficacy of clear aligners. Various parameters, such as fit, comfort, and wear resistance, are evaluated through clinical trials and feedback from dental professionals. Manufacturers often engage in in-house testing, and third-party evaluations to validate their processes and outcomes. By employing advanced technologies and methodologies, like Computer-Aided Design (CAD) and Computer-Aided Manufacturing (CAM), the precision of the aligners can be significantly enhanced.
Related articles: Introduce Global OEM clear aligner services
The commitment to rigorous quality control measures not only bolsters consumer confidence but also solidifies the manufacturer’s position in the competitive landscape of orthodontics. As the clear aligners market continues to grow, maintaining high standards of product quality remains an indispensable factor for success. Ensuring that each aligner produced is of the highest standard will contribute to improved treatment outcomes for patients worldwide.